KR 1000 TITAN: HEAVYWEIGHT CHAMPION FROM KUKA
A total of six KUKA heavy-duty robots are used for stacking heavy steel beams at Mannstaedt GmbH ready for onward transportation. With a few exceptions, the use of robots in steel production had previously been uncharted territory.
A total of six KUKA heavy-duty robots are used for stacking heavy steel beams at Mannstaedt GmbH ready for onward transportation. With a few exceptions, the use of robots in steel production had previously been uncharted territory.
ROBOT-BASED HANDLING: STACKING OF SPECIAL PROFILES WEIGHING UP TO 2.5 TONNES
Mannstaedt GmbH, based in Troisdorf in the German state of North Rhine-Westphalia, produces tailor-made special profiles. Used in the automotive industry and port construction, for example, the steel profiles can weigh up to 2.5 tonnes at a length of up to 26 meters. That already describes the first challenge that had to be met in implementing the solution: the handling of very heavy steel beams was previously not possible for robots. Six KUKA KR 1000 titan robots are now installed at Mannstaedt. Following delivery by conveyor, the special profiles are stacked by the robots in a space-saving manner. The stacks are then conveyed out of the robot station for shipment to the customers.
KUKA HEAVY-DUTY ROBOTS: STRONG AND PRECISE
The decisive advantage of the changeover: thanks to the robotic automation solution special profiles with a length of up to 26 meters - instead of the prior maximum of 16 meters - can now be produced. Six KR 1000 titan robots make this possible. The heavy-duty robots offer not only a very high payload capacity but also high repeatability even over greater distances.
SUCCESSFUL PROJECT: ROBOTS MEET THE EXPECTATIONS
"The system is an absolute success. With simplified methods, we have made production easier and more flexible," exclaims Marcus Haas, Plant Manager at Mannstaedt GmbH. The changeover has enabled his company to significantly increase the flexibility of production, which is reflected directly in an enlarged range of products. The success has prompted Mannstaedt to initiate new automation projects in the downstream production process.
Featured Product
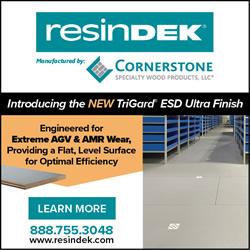
ResinDek® TRIGARD® ESD ULTRA FOR HIGH-TRAFFIC ROBOTIC APPLICATIONS
To maximize the productivity of an autonomous mobile robot (AMR) or automatic guided vehicle (AGV) deployment, it's critical to create the optimal environment that allows the vehicles to perform at their peak. For that reason, Cornerstone Specialty Wood Products, LLC® (www.resindek.com) created the TriGard® ESD Ultra finish for its ResinDek® engineered flooring panels. The TriGard ESD Ultra finish is ideal for high-traffic robotic applications characterized by highly repetitive movement patterns and defined travel paths.