Fly-off Provides Direct Comparison of Aerial Survey Drones
As the number of choices for drone based photogrammetry continue to grow it becomes increasingly difficult to determine which platform to select. A recent CH2M Hill sponsored fly-off provided a unique opportunity to compare between available platforms, and the resulting analysis reveals significant differences between leading systems.
The fly-off provided one of the first glimpses into the quality of data produced by each platform, and the effect that vehicle design differences have on image collection and the resulting post-processing. Even with a large number of participating systems, the cost-effective Black Swift Technologies SwiftTrainer system emerged as a leader in many categories.
In an effort to characterize the quality of drone data collects, CH2M Hill sponsored a fly-off between a selection of geospatial solution providers from across the nation. An 180 acre area of interest (AOI) was identified and sent to participants beforehand along with the locations of ground control points. The day of the event, each participant signed up for a flight time and was given the opportunity to perform a collect as per their usual routine. The data was then compiled and made available to all teams.
Preliminary results show a vast difference between leading platforms, specifically and most importantly the quality of information which can be derived from drone based imagery. First, the size of AOI demonstrated the value of fixed-wing systems. While multi-rotor systems are highly popular and valuable for limited areas, fixed wing solutions are well designed for mapping or surveying areas greater than 50 acres in size, and were the only vehicles able to cover the AOI in one flight while providing a significant overlap between pictures. Second, examination of the processed data from the fixed-wing systems revealed several issues that significantly impacted the accuracy of the resulting information. As an example, the errors present in the terrain height estimation from two of the platforms had a significant adverse effect on any sort of volumetric analysis.
Several key factors contributed to the errors, specifically the guidance algorithms, image triggering process, and vehicle design. The results of these differences between each UAS are readily apparent when examining the picture locations from each system, given that a uniform grid will provide the best post-processing results. Additional information, including plots of these picture locations, as well as a detailed analysis of the fly-off is available in this comprehensive white paper.
Featured Product
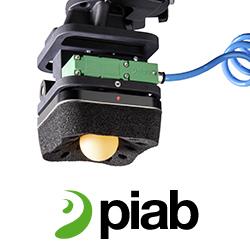