Temperature will be crucial to successfully powering the mobile robotics revolution
Reliable use of mobile robotics platforms in environments where temperatures reach extremes could be near impossible without a way to regulate battery temperature.
The rise of the robots has begun, although not in the way most science fiction films have predicted. Advances in industrial robotics and autonomous systems are seeing many new mobile robotics applications coming to the market. These are solutions which are fully mobile and therefore require their own on-board power. With applications ranging from warehouse robots moving pallets and picking orders, assisting with construction site work, all the way to unmanned aerial vehicles (UAVs) for security and surveillance, the range of possible functions this new technology can be channelled into is dazzling, and potentially endless.
The need for reliable, on board power is one of the potential limiting factors for these mobile systems. Fortunately, there have been major advances in energy storage driven in part by the boom in the automotive sector for electric and hybrid cars. This has resulted in huge improvements in energy density and, crucially, cost.
For advanced mobile robots, lithium ion (Li Ion) battery packs are the current best choice due to their high energy density and long cycle life when compared to more traditional solutions such as the lead acid batteries that have traditionally been used in industrial equipment. The performance improvement that can be gained through the implementation of Li Ion technology is huge. However, that performance can be negatively affected by one crucial thing in particular - temperature. If the cells of the battery become too hot or too cold, they can be permanently damaged and degrade much faster than expected. The result is a compromised or ultimately useless battery that will, in current and most projected markets, cost thousands to replace.
Reliable use of mobile robotics platforms in environments where temperatures reach extremes could be near impossible without a way to regulate battery temperature. Where its cold, charging is an issue; Li Ion batteries cant be fast charged when they are less than 5oC and cannot be charged at all at below 00C. Where its hot, the cells will degrade quickly if their temperature exceeds 45oC.
Now, cleantech firm AVID Technology is urging others to recognise the need to address the issue of battery temperature control in mobile robotics applications and has produced a white paper analysing current research findings in an attempt to identify the best method.
Ryan Maughan, managing director of AVID Technology Group Ltd, explains:
"Advanced, effective techniques for controlling battery temperature are essential if high performance mobile robots are ever to match the reliability, durability and performance that their applications demand.
"As the global market for these applications looks set to move up a gear we really need to apply ourselves to resolving this problem. Researchers have highlighted that we must be concerned not only with retaining ideal temperatures but with the method chosen to produce the cooling, as this affects the lifetime performance of the cells. The best method, according to studies, is still uncommon in the automotive industry, and, however complex it may be to introduce, this needs to change."
Based in North East England, AVIDs core expertise is the design of power electronics and motors used in electric propulsion systems with applications from automotive to UAVs. The company has significant experience in the design of battery systems and thermal management. AVID is now exploring how its technology can be best utilised to achieve the ideal high performance battery system for mobile robotic needs.
"We believe it is important to start looking at the details of such studies and how this should influence design sooner rather than later. Our white paper summarises leading research findings on the best methods of temperature control and examines current cooling system design and how these can - and must - be improved."
A market leader in the design and manufacture of electrified powertrain systems for the electric and hybrid vehicle industry, robotics and aerospace, AVID has recently invested in a state-of-the-art electronics surface mount (SMT) manufacturing facility and new test equipment, set to increase production of automotive electronics and powertrain technology, and enable the company to diversify into the robotics and power generation industries.
To read the new white paper on the most efficient method of battery cooling visit:
http://avidtp.com/what-is-the-best-cooling-system-for-electric-vehicle-battery-packs/.
Featured Product
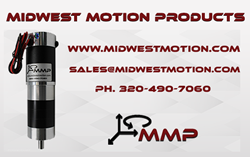