IMTS Is the Additive Manufacturing Destination for 2022
The people and companies propelling AM forward will connect at IMTS 2022 – The International Manufacturing Technology Show, which is now considered a primary AM destination. IMTS 2022 will showcase AM solutions as part integrated manufacturing technology offerings in the Metal Removal, Quality Assurance, CAD/CAM, and other Technology Pavilions covering 1.1 million sq. ft. of exhibit space.
McLean, Va., (October 28, 2021) - Just as space sparks the imagination, additive manufacturing (AM) is sparking new solutions while also solving mainstream industrial challenges in ways unimaginable just a few years ago, such as 3D printed components for NASA's Artemis moon program. The people and companies propelling AM forward will connect at IMTS 2022 - The International Manufacturing Technology Show, which is now considered a primary AM destination.
"The pace at which AM technologies accelerate makes IMTS 2022 a must-attend event," says Peter R. Eelman, vice president & CXO at AMT - The Association For Manufacturing Technology, which owns and produces IMTS. "Visitors will see AM solutions for production and high-volume part applications, tooling, workholding and fixturing that improve performance, lower lifecycle costs, and help reshore production. They'll also be able to meet people pushing the boundaries of AM, including multiple technologies and components being developed for NASA."
Benjamin Moses, director, technology at AMT, says that, "IMTS exhibitors and AMT members have developed new additive systems with extremely large print volumes, yet they deliver the deposition precision and repeatability that NASA demands due to in-situ metrology and closed-loop controls."
Developments include an 11-ft.-tall main rocket engine nozzle liner printed from JBK-75 (a stainless steel hydrogen-resistant superalloy) and a scanning electron beam microscope combined with an electron beam 3D metal printing system for replicating parts in space (see story).
"Wire AM systems developed for aerospace parts are well-suited for tooling and other large components," comments Moses. "In addition, modeling software developed to validate these concepts will help other industries build AM parts faster, at lower cost and with high quality."
Tank Teamwork
To create solutions for complex challenges, companies with AM solutions are collaborating to win contracts by coordinating with best-in-class technologies. As an example, a team of subcontractors from Ingersoll Machine Tools utilizing their MasterPrint® product offering and integration abilities (large scale additive machines), Siemens (digital twin software) and MELD Manufacturing (the patented thermo-mechanical MELD® process) will help build the world's largest metal 3D printer as part of U.S. Army's Jointless Hull Program. The system will have a print volume of 20 x 30 x 12 ft. — large enough to print the next generation of main battle tank hulls and other combat vehicles, as monolithic hulls have well-established advantages in survivability and weight savings.
"Teamwork solved a real market problem, and that's a great reason to attend a show like IMTS," says Jason Melcher, vice president of sales, Ingersoll Machine Tools, Inc. "From a collaboration standpoint, we attend conferences and trade shows specifically to listen to a particular technology presenter or visit a particular exhibit. What we don't know is who else we'll meet at the show — yet we always find people with solutions that we haven't been able to even think about. Today, there's too many problems and too many opportunities to tackle on our own. We as an industry need to find partners, and IMTS and its conferences are great venues for doing so."
Surging Demand
AM education opportunities at IMTS 2022 include the next edition of the Additive Manufacturing Conference presented by Additive Manufacturing Media, which is co-located with IMTS during show years. The AM Pavilion and AM Conference are located across the main concourse from each other in the West Building of McCormick Place (see floor plan with exhibitors).
"In the midst of what appears to be long-term supply chain issues and a greater emphasis on reshoring, we are now in a different place with additive manufacturing," says Peter Zelinski, editor-in-chief of Additive Manufacturing Media as well as Modern Machine Shop magazine. "Using 3D printing to make both end-use parts and tooling is now recognized for the part it plays in an agile production strategy. It is no longer the case that it's a novel and interesting development that AM has a place at IMTS. Instead, it's now vital that IMTS includes AM, because attendees need this capability and know they need it."
"The manufacturing economy has grown for 16 consecutive months, and the challenges manufacturers and job shops face have never been greater," says Eelman. "The most efficient way to increase productivity per employee and create a lean supply chain is by implementing digital technologies such as additive manufacturing, and IMTS showcases the most complete breadth and depth of digital technologies available."
Featured Product
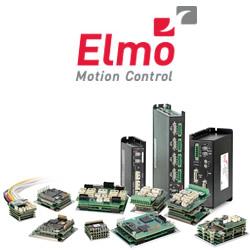