New Automation for Laser Tube Cutting from TRUMPF
Laser tube cutting machines can now automatically convey cut tubes to an automation system, which then sorts the parts or delivers them to the next production step for further processing. This automated unloading system provides the missing link in the chain that enables every automation of every step in the tube fabrication process, including laser tube cutting. The solution is available for TRUMPF's 5000 and 7000 series TruLaser Tube laser cutting machines and is designed to boost productivity and free operators for other tasks.
Farmington, Conn., July 31, 2024 - TRUMPF Inc. has announced a new automated unloading system for its laser tube cutting machines. Laser tube cutting machines equipped with the "automated unloading interface with longitudinal belt conveyor" can automatically convey cut tubes to an automation system, which then sorts the parts or delivers them to the next production step for further processing. The automation solution, which is designed to prevent errors and reduce the operator's workload, is available for TRUMPF's 5000 and 7000 series TruLaser Tube laser cutting machines.
"This new automation technology is another example of how TRUMPF provides solutions that address the real-world requirements of companies in the metal fabrication industry," says TRUMPF Inc. Executive Vice President Burke Doar. "Laser tube cutting involves a high operator workload, which can be very challenging for many companies. Our solution helps companies tackle the shortage of skilled workers while also improving capacity utilization. The result is higher productivity and greater competitiveness."
Compared to many other technologies, laser tube cutting requires significant operator involvement. TruLaser Tube machines are highly productive, which means a production worker needs to be available at regular intervals to remove and sort the cut tubes. With skilled staff in short supply, it can be hard for fabricators to find someone to carry out this task. In addition, the cut tubes tend to be large and unwieldy, so workers are often reluctant to take on this job. TRUMPF's automated unloading system helps solve this dilemma.
Ideal for medium and high-volume production
In machines equipped with the new solution, the laser cut tubes are automatically deposited on a belt conveyor. The conveyor transports the parts to the automation system's safety enclosure. Here, the parts are retrieved by a separate machine known as an integrator, which could be a robot or some other handling device. TRUMPF uses integrators from well-known partners, such as Starmatik and Transfluid, for part retrieval and handling.
None of the automation obstructs or limits the open concept of the laser cutting machine: users are still free to unload parts manually, an option that continues to be particularly advantageous for small batch sizes and intermediate products. TRUMPF's automated unloading system also features a digital interface that transfers all relevant information about the parts to the integrator. TRUMPF's Programming Tube software makes this data available to the integrator automatically via the TruLaser Tube's digital interface. This data makes the next stage simpler, for example by enabling the Starmatik robot to sort cut parts or convey them directly to the next step in the process without having to teach individual positions. This digitalization solution also saves time and reduces the possibility of errors.
Fully automating the tube process chain
TRUMPF's automated unloading system is a particularly good choice for medium and high-volume manufacturers, as well as for job shops that handle orders of various sizes. Typical applications include furniture, fitness machines and agricultural machinery.
TRUMPF's automated unloading system is the final link in the chain that enables every step in the tube fabrication process to be automated, including laser tube cutting. The company's automated loading system, which enables raw material to be taken directly from storage and automatically loaded into the machine, has already been on the market for some time. TRUMPF can also help users to automate their tube-bending and welding processes. To achieve these advances in the tube-processing chain, TRUMPF works with well-known industry partners, including Starmatik, Transfluid and STOPA.
Featured Product
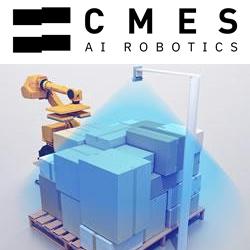