Implementing xPump – AI/ML Based Pump Monitoring & Predictive Maintenance System on the Dry Screw Vacuum Pumps DynaSeal Liquid Ring Vacuum TRO015H
In today's fast-paced industrial environment, equipment reliability is paramount. The efficiency of manufacturing processes hinges on the ability of machinery to operate without unexpected failures. Ensuring that vacuum pumps function optimally is critical for industries relying heavily on vacuum systems, such as semiconductor manufacturing and pharmaceutical production. In this context, the implementation of advanced monitoring systems like xPump, which utilizes Artificial Intelligence (AI) and Machine Learning (ML), can significantly enhance equipment reliability. This blog explores how xPump can be integrated with DynaSeal Liquid Ring Vacuum TRO015H pumps to revolutionize maintenance strategies.
Understanding the Importance of Equipment Reliability
The Cost of Downtime
Equipment failures can lead to significant downtime, resulting in lost productivity and increased operational costs. According to studies, unplanned downtime can cost manufacturers thousands, if not millions, of dollars per hour. For vacuum pumps, this can mean not only lost production time but also potential damage to products and processes.
The Role of Predictive Maintenance
Predictive maintenance aims to foresee equipment failures before they occur. By analyzing data from equipment in real-time, organizations can schedule maintenance activities at optimal times, thereby avoiding unexpected breakdowns. This proactive approach reduces the overall maintenance costs and extends the life of the equipment.
Introducing xPump: An AI/ML-Based Solution
What is xPump?
xPump is an innovative pump monitoring and predictive maintenance system that leverages AI and ML technologies. By gathering and analyzing data from vacuum pumps, xPump provides actionable insights that can enhance performance and reliability.
Key Features of xPump
Real-Time Monitoring: xPump continuously monitors the operational parameters of the DynaSeal Liquid Ring Vacuum TRO015H, including pressure, temperature, and flow rates.
Data Analytics: The system employs advanced data analytics to identify patterns and anomalies in pump performance, allowing for the early detection of potential issues.
Predictive Algorithms: Using ML algorithms, xPump can predict when a pump is likely to fail based on historical data and current operating conditions.
User-Friendly Interface: The intuitive dashboard allows operators to visualize pump performance and receive alerts for any anomalies.
Implementing xPump on DynaSeal Liquid Ring Vacuum TRO015H
Step 1: Initial Assessment
Before implementation, it is crucial to conduct an initial assessment of the existing vacuum pump setup. This includes evaluating the current performance metrics of the DynaSeal TRO015H and identifying any recurring issues. Understanding the baseline performance is essential for comparing improvements post-implementation.
Step 2: Integration with Existing Systems
Integrating xPump with existing monitoring and control systems is key to leveraging its full potential. The system can be connected to the DynaSeal vacuum pumps via IoT devices that facilitate data transfer. This integration ensures seamless communication between the pumps and the xPump analytics platform.
Step 3: Data Collection and Analysis
Once integrated, xPump begins to collect data in real-time. This data is analyzed to establish performance benchmarks and identify any deviations from normal operation. By employing ML algorithms, the system can continuously learn from this data, improving its predictive capabilities over time.
Step 4: Setting Up Alerts and Notifications
Configuring alerts and notifications is a critical step in ensuring timely interventions. xPump can be set up to notify operators of any anomalies, such as unexpected fluctuations in pressure or temperature, which may indicate potential failures. Early alerts enable maintenance teams to take proactive measures before a complete breakdown occurs.
Step 5: Continuous Monitoring and Improvement
The implementation of xPump is not a one-time event but an ongoing process. Continuous monitoring allows for real-time adjustments and improvements to maintenance strategies. Regularly reviewing performance data helps identify new trends and areas for enhancement.
Benefits of Implementing xPump
Improved Reliability and Uptime
By utilizing predictive maintenance strategies, organizations can significantly reduce unplanned downtime. xPump's ability to predict failures allows maintenance teams to address issues before they escalate, ensuring continuous operation of the DynaSeal vacuum pumps.
Cost Savings
Investing in predictive maintenance technology like xPump can lead to substantial cost savings. By minimizing downtime and reducing emergency repairs, companies can optimize their maintenance budgets and improve their bottom line.
Enhanced Performance
With real-time monitoring and analytics, the DynaSeal Liquid Ring Vacuum TRO015H can operate at peak performance levels. The insights provided by xPump enable operators to optimize processes and improve overall efficiency.
Extended Equipment Lifespan
Regular maintenance based on predictive analytics helps extend the lifespan of equipment. By identifying potential issues early, organizations can avoid catastrophic failures that could lead to costly repairs or replacements.
Case Study: Successful Implementation of xPump
To illustrate the effectiveness of xPump, let's consider a case study involving a semiconductor manufacturing facility that implemented xPump on their DynaSeal vacuum pumps. Before the integration, the facility experienced frequent pump failures, resulting in costly downtime and production delays.
After implementing xPump, the facility noted a 30% reduction in unplanned downtime within the first six months. xPump's predictive capabilities enabled maintenance teams to schedule repairs proactively, leading to improved efficiency and significant cost savings.
Conclusion: A Call to Action
In an era where equipment reliability is crucial for operational success, adopting advanced technologies like xPump can transform maintenance strategies. Organizations can enhance reliability, reduce costs, and improve efficiency by implementing AI and ML-based monitoring systems on DynaSeal Liquid Ring Vacuum TRO015H pumps.
If you are ready to improve equipment reliability, consider implementing xPump today. Don't wait for equipment failures to disrupt your operations; act now to secure your production processes with cutting-edge predictive maintenance solutions. Contact us to learn more about how xPump can benefit your facility and start your journey toward enhanced equipment reliability!
Featured Product
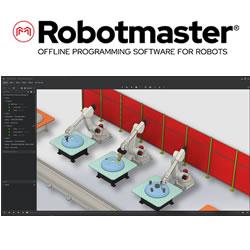