New Laser Cutting Modulating Strategy Tested with Mikrotron High-Speed Cameras
Because of its non-contact characteristics, this technique prevents mechanical stress on the workpiece while maintaining extremely high cutting precision. Today it is widely used in aerospace, construction, and automotive manufacturing, among other industries, and is typically controlled by a CNC for accuracy and repeatability.
Gilching, Germany, February 17, 2025 -- First invented in 1965, laser cutting technology works by directing the output of a focused laser beam onto a metal workpiece, vaporizing or melting the metal and creating a cut edge. Because of its non-contact characteristics, this technique prevents mechanical stress on the workpiece while maintaining extremely high cutting precision. Today it is widely used in aerospace, construction, and automotive manufacturing, among other industries, and is typically controlled by a CNC for accuracy and repeatability.
IMPROVING CUTTING QUALITY
Modulating a laser beam intensity's distribution optimizes energy delivery to the process zone, resulting in better cutting speed, cut edge quality, and cut kerf geometry. The conventional approaches to modulating is Static Beam Strategy (SBS) and the Dynamic Beam Shaping (DBS) method.
Scientists at KU Leuven, an international research community located in Leuven, Belgium, recently conducted a comprehensive investigation into a new strategy of modulating beam intensities they termed "dynamic intensity modulation" and compared it to SBS and DBS while cutting 15mm thick mild steel. This novel approach modulates the intensity distribution using oscillation speed alteration.
Experiments were conducted using an industrial 2D flat-bed laser cutting machine featuring 4kW laser power and equipped with a multimode fiber laser source producing a top-hat intensity distribution. The laser beam was guided to the process zone via an optical fiber.
To gain visual insights into the dynamic flow of molten material within the cut kerf, the scientists relied on a Mikrotron EoSens 1.3 Megapixel CMOS camera equipped with a Navitar Zoom 7000 lens. An OD 6 notch filter was placed in front of the camera lens to remove reflected or scattered laser light.
The Mikrotron camera's region of interest was configured to 160 x 370 pixels with the exposure time fixed at 10µs, resulting in a frame rate of 5000 frames per second. Dynamic range adjustment prevented overexposure, therefore enhancing visualization of the crude contrast between the cut edge and the molten material inside the kerf.
Once captured, the cut edge images were scanned at 100x magnification with an optical microscope. An algorithm was applied to measure the dross area using the 2D images. Additionally, 3D images were generated to assess the roughness of the cut edge.
Testing dynamic intensity modulation on the cutting of mild steel indicated a notable enhancement in the cut edge quality compared to either the SBS or DBS strategies. The dynamic intensity modulation technology, according to the scientists, can also be used for other laser processes like hardening and welding.
Learn more at www.mikrotron.de or www.svs-vistek.com.
1. Laser cutting using dynamically modulated intensity distribution, January 2024, Procedia CIRP 124:716-719, DOI: 10.1016/j.procir.2024.08.209, Masoud Kardan, Sylvie Castagne, Joost Duflou
Featured Product
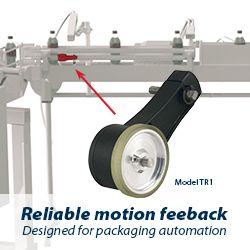