Industrial Robot Controllers: The Backbone of Smart Manufacturing and Automation
As industries increasingly turn to automation, Industrial Robot Controllers (IRCs) have emerged as the indispensable brains of robotic systems. From assembly lines in automotive manufacturing to the intricate precision required in pharmaceutical production, these advanced controllers are essential for ensuring efficiency, precision, and safety. In an ever-evolving landscape of industrial automation, understanding the pivotal role of IRCs is key to grasping the future of manufacturing. Here, we delve into the components, functionality, and emerging trends that define the world of industrial robot controllers.
What is an Industrial Robot Controller?
An Industrial Robot Controller (IRC) serves as the control unit for robotic systems, orchestrating movement, task execution, and interaction with external systems. Essentially, the IRC is the central processing unit (CPU) of the robot, allowing for precise movement control, system diagnostics, and integration with other automation equipment, including Programmable Logic Controllers (PLCs) and Manufacturing Execution Systems (MES).
The IRC connects the robot's mechanical arms to its intellectual capabilities, enabling a wide variety of industrial applications from welding and material handling to complex assembly tasks. Without it, even the most advanced robotic arm would be unable to carry out its intended functions.
Industrial Robot Controller Industry Overview
The industrial robot controller market is poised for significant growth in the coming years. In 2024, the market is expected to reach a size of USD 1,086 Million and is projected to expand to USD 2,619 Million by 2034, reflecting a CAGR of 9.2% from 2024 to 2034. This growth highlights the increasing demand for automation in various industries, driven by the need for enhanced precision, productivity, and scalability in manufacturing processes.
How does the controller function?
- The controller operates by receiving commands from a program or console, which it then converts into precise movements of the robot's joints and actuators.
- It continuously monitors feedback from the robot to ensure accurate positioning and motion.
- Additionally, the controller manages emergency stop functions and safety protocols to prevent collisions and ensure operator safety.
Key Components of an Industrial Robot Controller
At the core of every industrial robot controller is a sophisticated system of hardware and software that ensures seamless integration, precision, and safety.
- Central Processing Unit (CPU): This acts as the brain of the controller, processing complex algorithms to manage the robot's actions in real-time.
- Input/Output (I/O) Systems: These enable the robot to interact with external sensors and devices, allowing it to respond to environmental conditions and perform feedback loops for improved accuracy.
- Safety Modules: Built-in safety features are critical in industrial settings. Emergency stop mechanisms, force sensors, and automatic shutdown protocols ensure that robots operate within safe parameters, mitigating risks to both human operators and equipment.
- Operator Interface: Whether through a teach pendant (a handheld device) or a graphical user interface (GUI), operators can program the robot, modify its behavior, and troubleshoot in real-time.
- Communication Ports: As industrial robots are increasingly integrated into the broader Internet of Things (IoT) ecosystem, these controllers feature advanced communication capabilities, including Ethernet, wireless, and fieldbus protocols. This enables remote monitoring, diagnostics, and real-time feedback from various systems.
The Role of Software in Industrial Robot Controllers
In addition to the hardware that powers the system, the software embedded within robot controllers plays a crucial role in defining the robot's behavior. The programming languages used to control robots such as RAPID, KUKA Robot Language (KRL), and Robot Studio allow operators to instruct the robot in a series of precise steps, including task scheduling and motion planning.
Moreover, simulation tools allow operators to pre-program robots in a virtual environment, ensuring optimal movement patterns and identifying potential errors before deploying the robot in a live setting. With the rise of artificial intelligence (AI), robots are also becoming capable of learning from their surroundings, improving their adaptability over time.
Benefits of Using Robot Controllers
The integration of robot controllers in manufacturing systems offers several key advantages:
- Cost-effective: Robot controllers automate various processes, significantly reducing the reliance on human labor. This leads to lower labor costs and a boost in overall productivity.
- Superhuman Precision and Consistency: Robots, when properly maintained and calibrated, perform repetitive tasks with remarkable precision and consistency. Unlike humans, they don't tire, lose focus, or become distracted, ensuring uniform results every time.
- Flexible: While robots are typically programmed for specific tasks, their controllers can be easily reprogrammed to accommodate changes in the manufacturing process or production line. Additionally, robots can be deployed in hazardous environments where human intervention might be dangerous.
- Scalable: Robot controllers allow for easy scalability in manufacturing operations. As demand increases, more robots and controllers can be added to the system, enabling faster production and higher output to meet growing needs.
Applications Across Industries
From automotive assembly lines to warehouse logistics, industrial robot controllers are revolutionizing industries across the globe. Here are some prominent examples:
- Automotive Manufacturing: In an industry where speed, precision, and scalability are crucial, IRCs manage robots that perform tasks like welding, painting, and part assembly with near-perfect accuracy.
- Electronics and Semiconductor Production: The precision required in electronics assembly demands a high level of control. Robot controllers in these environments guide robots to handle delicate components, assemble microchips, and automate testing processes.
- Pharmaceutical and Food Processing: In sterile environments, robots, guided by IRCs, handle tasks like packaging, labeling, and even filling pharmaceuticals or food products into containers, ensuring safety, hygiene, and consistency.
- Logistics and Warehousing: Automated guided vehicles (AGVs) and robotic arms equipped with advanced controllers are increasingly deployed to pick, pack, and sort products in distribution centers, speeding up the supply chain while reducing errors.
Industrial Robot Controller Market Top Companies:
- Stäubli International AG
- Mitsubishi Electric Corporation
- OMRON Corporation
- DENSO Wave Incorporated
- SEPRO Group
- WAGO
- Motion Controls Robotics Inc.
- NexCOM Inc.
- Wynright Corporation
- KUKA AG
- Yaskawa Electric Corporation
The Future of Industrial Robot Controllers
Looking to the future, Industrial Robot Controllers are poised to undergo a remarkable transformation. As Industry 4.0 continues to take shape, the following trends are expected to dominate the field:
- AI and Machine Learning Integration: The future of industrial automation lies in robots that can learn from their environments. AI-driven controllers will enable robots to optimize their performance based on data inputs, improving accuracy and reducing the need for human intervention.
- Edge Computing: As the need for real-time decision-making becomes more critical, edge computing will allow industrial robots to process data on-site rather than relying on cloud servers, reducing latency and enhancing performance.
- Cobots and Human-Robot Collaboration: The rise of collaborative robots (cobots) robots designed to work alongside human operators will drive innovation in robot controllers, allowing for safer, more intuitive interactions between humans and machines.
- Cybersecurity: As industrial systems become more interconnected, the importance of securing robot controllers against cyber threats will become paramount. Robust security protocols will be essential to prevent malicious attacks and ensure the safety of sensitive data and processes.
- Cloud-based Control Systems: The future will see a rise in cloud-based industrial robot controllers that allow for centralized management, remote diagnostics, and seamless data sharing across distributed operations.
Source: https://www.statifacts.com/outlook/industrial-robot-controller-market
𝐂𝐨𝐧𝐭𝐚𝐜𝐭 𝐔𝐬:
Ballindamm 22, 20095 Hamburg, Germany
sales@statifacts.com
𝐀𝐛𝐨𝐮𝐭 𝐔𝐬:
Statifacts is a leading provider of comprehensive market research and analytics services, offering over 1,000,000 market and customer data sets across various industries. Their platform enables businesses to make informed strategic decisions by providing full access to statistics, downloadable in formats such as XLS, PDF, and PNG.
Featured Product
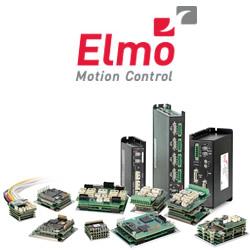