Furrion Showcases World's First Exo-Bionic Racing Mech in Motion and Unveils X1 Mech Racing
Furrion's Exo-Bionic development team unveiled a short film revealing the first look of Prosthesis in motion and the launch of a brand-new sport-- the X1 Mech Racing League.
SCHAFT Unveils Awesome New Bipedal Robot at Japan Conference
From Evan Ackerman at IEEE Spectrum: Right now, the New Economic Summit (NEST) 2016 conference is going on in Tokyo, Japan. One of the keynote speakers is Andy Rubin. Rubin was in charge of Google’s robotics program in 2013, when the company (now Alphabet) acquired a fistful of some of the most capable and interesting robotics companies in the world. One of those companies was SCHAFT, which originated at the JSK Robotics Laboratory at the University of Tokyo...
... SCHAFT co-founder and CEO Yuto Nakanishi climbed onstage to introduce his company’s new bipedal robot. He explains that the robot can climb stairs, carry a 60-kg payload, and step on a pipe and keep its balance. It can also move in tight spaces, and the video shows the robot climbing a narrow staircase by positioning its legs behind its body (1:22). In a curious part of the demo (1:36), the robot is shown cleaning a set of stairs with a spinning brush and what appears to be a vacuum attached to its feet... ( article )
Festo's R&D Timeline - Part 4
More interesting stuff from Festo - ExoHand, CogniGame, SmartInversion, NanoForceGripper
Festo's R&D Timeline - Part 3 - 2010 & 2011
Part 3 includes more bionic robots like the smartbird and a handler modeled after an elephant trunk.
Festo's R&D Timeline - Part 2 - 2007-2009
More fascinating bionics projects from Festo.
Festo's R&D Timeline - Part 1
Since 2006 Festo has been developing and supporting projects and test objects whose basic technical principles are derived from a wide variety of principles found in nature.
Records 1 to 6 of 6
Featured Product
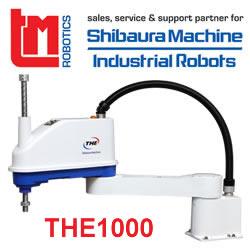
TM Robotics - Shibaura Machine THE SCARA range
The THE range from Shibaura Machine is an extensive line up of SCARA robots. Available in four arm lengths THE400 (400mm), THE600 (600mm) and the most recent THE800 (800mm) and THE1000 (1000mm), this range is suitable for assembly, handling, inspection and pick and place processes in varied industrial applications. The THE1000 boasts a 20kg payload capacity and an impressive 0.44 second cycle time, providing high speeds for processes with large components. In fact, the range has been recognised for as the price-to-performance leader compared to other SCARA models in its price range due to its impressive speed versus payload capacity.